Software, Electrical, Mechanical Design and Manufacture.
Automated Test
Automating test increases the consistency of manufacture and testing. Peak Production specialises in the automation of functional test. Using automation reduces test time and increases consistency of testing while allowing qualified people to do other more skilled work. We use various methods to automate movement within systems. These include pneumatics, electrical powering of devices and sensors to detect limits of travel and position of products before proceeding with further tests.
Automating
At the centre of the automated system is a computing device. This could be a PC, specialised PXI rack, embedded controller or a PLC. Using output modules to set actuators and input modules for detection the system runs automatically. With the use of multiplexor and relay modules, signals can be routed to test equipment, reducing the number of measurement devices needed within the system. For the control system to function, software is needed to control and monitor connected devices. Further enhancements could include network communications to databases, websites and other control systems. Software is programmed at our facilities in Letchworth Garden City by Peak Production using the following platforms:
Typically 10U or less with a base unit beneath the work surface connected via an umbilical cable to a work surface test enclosure or fixture.
- Base unit encloses and protects test equipment
- Safety interlocking supports high voltage requirements
- Multiple sizes and options available
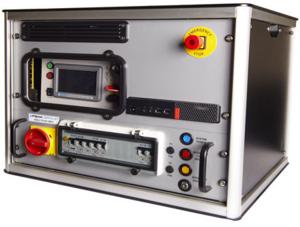
Trolley Based Solution
Entry level option for standalone portable test solutions, extended width chassis gives full use of U space and easy access for calibration and service while still allowing passage through a stand door.
- Interface Options
- Custom harness interface
- Umbilical to Test Enclosure/Fixture
- Mass interconnect interface
- Enhanced Air flow
- Large hinged doors allowing access
- Enhanced space for easy wiring
- Integrated Keyboard Tray
- Customisable panels
- Power box and safety circuits
- 14U internal capacity
Test Desk
Expansion on the Test Trolley giving more internal space and extended work surface with fixture guide rails, while still allowing passage through a stand door
- Mass interconnect interface
- Fixture slides and interface
- Enhanced Air flow
- Large hinged doors allowing access
- Enhanced space for easy wiring
- Integrated Keyboard Tray
- Customisable panels
- Power box and safety circuits
- Full depth 14 U capacity
- Part depth 9 U capacity
Reinforced exterior frame encloses a standard 19” sub frame giving a robust and reliable solution that allows full utilisation of U space with easy access for calibration and service. Available as standard width or extra wide to accommodate all ancillary equipment. Optional removable Fixture table supports all interfacing requirements.
- 36U to 42 U capacity
- 2 width options
- Mass interconnect interface
- Fixture slides and interface
- Enhanced Air flow
- Large hinged doors allowing access
- Enhanced space for easy wiring
- Customisable panels
- Power box and safety circuits
- Optional removable Fixture table with
- integrated Keyboard Tray
- Fully customisable
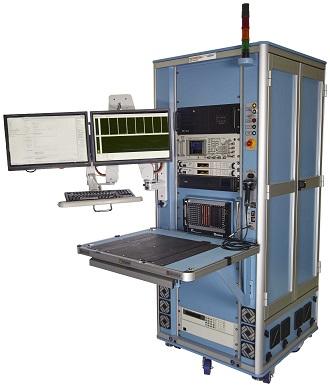
Dual Rack Solution
Extra reinforced exterior frame encloses two standard 19” sub frames with three extension areas to support wiring and ancillary equipment ensuring all U space is utilised with easy access for Calibration and Service. Optional removable Fixture table supports all interfacing requirements.
- 2 x 37U to 42 U capacity
- Mass interconnect interface
- Fixture slides and interface
- Enhanced Air flow
- Large hinged doors allowing access
- Enhanced space for easy wiring
- Customisable panels
- Power box and safety circuits
- Optional Fixture table with integrated Keyboard Tray
- Fully customisable
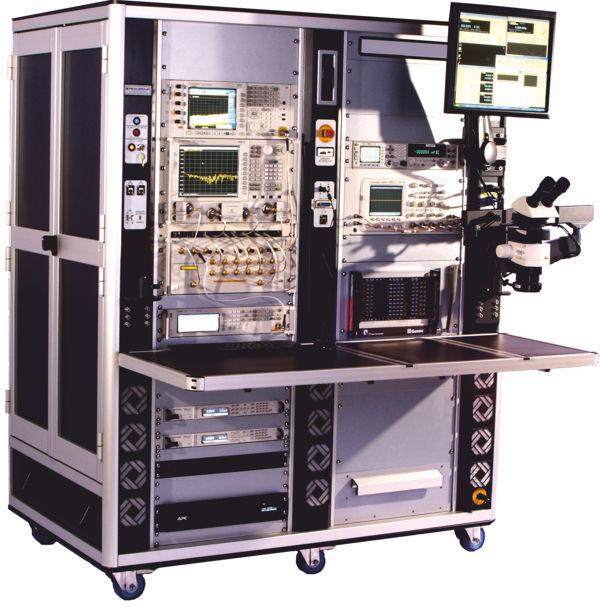
Custom Robot based solutions
Peak Production takes 35 years of test solution experience and integrates it seamlessly with the latest robot solutions. After a holistic review of the customer requirements Peak Production selects from several robot vendors the appropriate robot type to achieve the desired speed, handling and flexibility to not only meet our customers’ requirements today but to future proof the solution for their requirements tomorrow.
Peak Production offers solutions from simple standalone collaborative robots to complex integrated multirobot production lines.